Modelling: An Introduction to Silicone Rubber Moulding
Silicone rubber moulds are commonly used to produce small batch castings of jewellery and small pieces of silverware. This article is part of a series on different approaches to modelling and what you need to be aware of.
Casting is a process which is commonly used but not always understood. Whilst it is important for craftspeople to find themselves a trusted casting workshop, having an understanding of the processes and principles being used will aid you to discuss your work requirements with your chosen casting technician and to analyse the quality of the resulting work.
Having been modelling, sculpting and casting a range of high-quality items for over 50 years Mark Gartrell FIPG has established himself one of the UK's most adaptable workshops with the ability to design, model, cast, silversmith, chase and finish pieces in-house. And it is Mark's ability to be able to analyse each design and successfully select the most relevant processes to use which have allowed Mark to produce a gamut of work.
In this article Mark discusses the benefits of silicone rubber moulds for casting purposes.
“Silicone cold-moulds all modelling media by a process of catalytic curing, from the hardest of metals and stones to the softest of waxes. Its power to creep into the finest detail is phenomenal.”
What are the benefits of silicone rubber moulding?
Silicone cold-cure rubber moulds all modelling media by a process of catalytic curing, from the hardest of metals and stones to the softest of waxes. Its power to creep into the finest detail is phenomenal. This can, however, be a disadvantage with grained material like wood, where it creeps into and combines with the surface.
To counteract this, I smear such surfaces with petroleum gel using the finger and a soft sable brush to access restricted areas. Silicone itself needs no stop-off medium as casting waxes do not adhere to it, which is a great advantage. It is supplied in a wide variety of grades, from the everyday air curing bath sealant to a powder filled heat resistant silicone designed to make reusable pewter casting moulds. Many manufacturers make this product and reference to their data sheets will guide you to the material that best suits your needs. Tear strength and hardness varies greatly from product to product.
The addition of a thixotropic catalyst additive speeds the curing time of painted-on silicone skins, intended to have plaster back-ups for strengthening support. Painted on silicone would otherwise just ooze off the surface of your sculpture. I practise a style of box moulding to replace skin and plaster moulds for medium sized moulds. This is an extension of jewellery injection rubber moulding up to large sizes like 30cms x 10cms x 20cms.
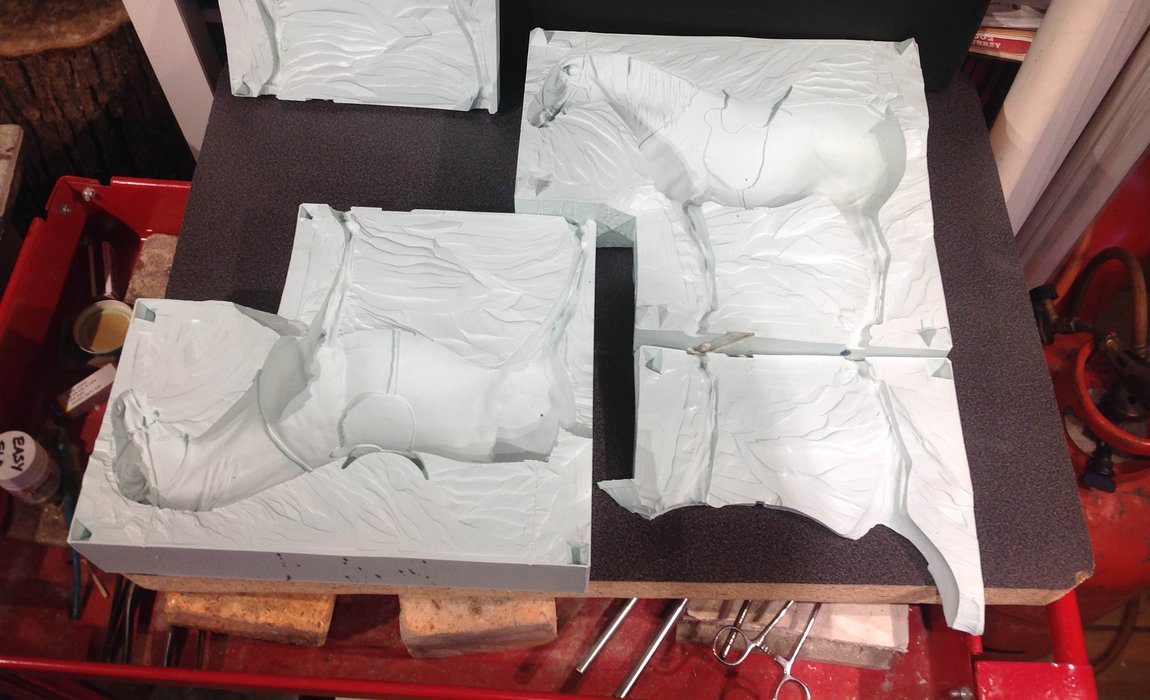
These macro sizes are moulded or poured into MDF bespoke boxes. This is justified by the economy of man hours employed and came about for projects which required both silver and bronze waxes to be pulled from the same mould. This process is ultimately self-limiting as the larger the mould, the heavier it becomes and therefore too unwieldy for pour in/out.
This kind of mould is ideal for painting up wax as the mould sits solidly on the workbench without rocking as plaster back-ups do. The use of this process is a question of scale and trade-offs, but up to medium size I have found real advantages to commend this style of moulding.
My model is complicated. How does moulding work for this?
The images above and below show a silicone rubber cut into multiple portions all with location pyramids in each corner. These pyramids ensure that the mould goes back together accurately and prevents movement as wax is injected into it under pressure. I normally decide to cut larger or more technical moulds into multiple pieces in order to make the removal of the wax easier and thus avoiding damage to it in the process. The importance of this is demonstrated perfectly by both the Copenhagen mould above, which due to its size required extra care, and the handle mould below, where left and right parts of the mould have further cuts that cannot be seen, which follow the acanthus leaves down into the rubber to permit easy withdrawal of the wax.
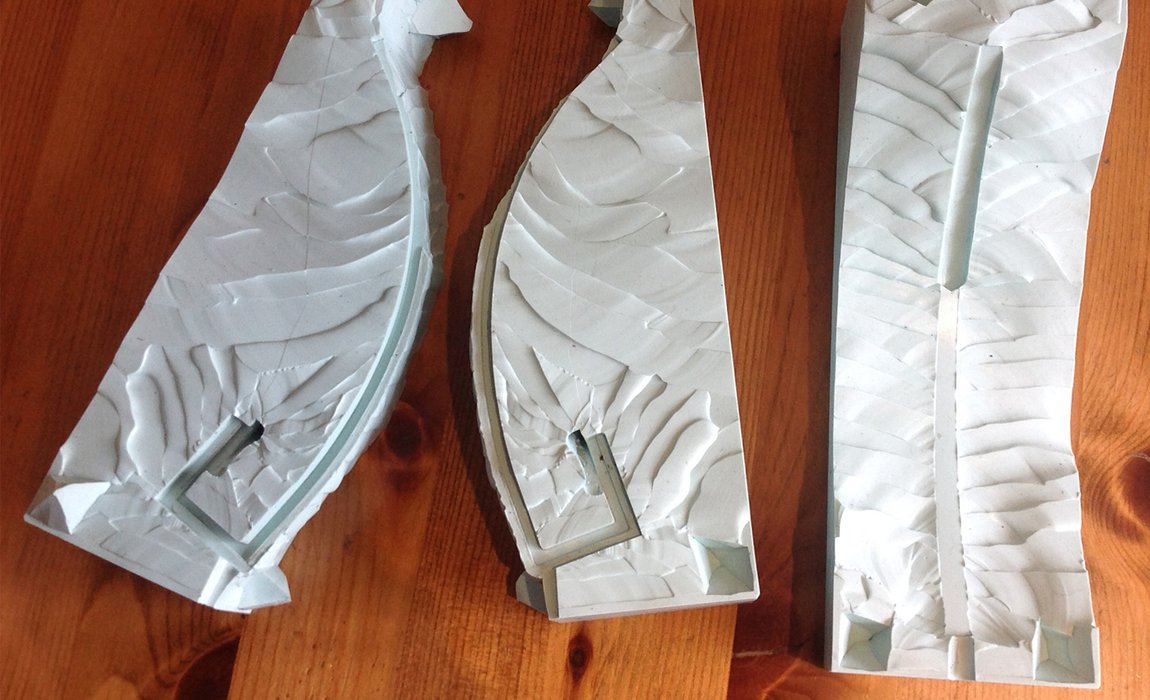
As the complexity of models increases so does the moulding and the number of pieces required to divide the mould into. We will not stray too far into this area of production as this article is primarily concerned with modelling.
The reason I have not discussed hot, pressure cured rubber moulding is that this is more appropriate to multiple production of jewellery where the mould is taken from a metal master. Here we are at the preceding stage where we don't yet have a metal master. Furthermore, when injecting larger sculptures, I find that silicone permits larger casting waxes to be produced very well. The two different rubber media sit comfortably together, both serving slightly different purposes and it is greatly to our advantage to have these to call upon as is needful.
Conclusion and further information
The complexity, scale and materials to be used will all have an impact on your work when casting. This article should have explained the benefits of using cold silicone rubber moulds within your work and there is further information to be found on modelling within the Modelling article series.
And don't presume that you must do it all yourself. In increasing your understanding of some of the materials, processes and techniques that Mark has encountered throughout his career, you are better able to make the right production decisions for yourself and, where required, find the right craftsperson for the job. Good luck!
There are many reputable sources of information relating to the jewellery, silversmithing and allied industries. Whether you are trying to find information on technical skills, processes, materials, makers or inspiration some resources relating to modelling can be found below:
The Goldsmiths’ Company Library relates specifically to gold and silversmithing, jewellery, assaying and hallmarking, precious metals, and the City of London and its guilds. The Library includes 8,000+ books and 15,000+ images, magazines, periodicals and journals, technical guides, films, special research collections, design drawings produced during the early and mid-twentieth century by British or UK-based craftspeople and subject files on a wide range of industry related topics. The Library is also responsible for the Company’s archives, which date back to the 14th century.
Modelling related articles include: