How to: Make Your Space Creative, Safe and Legal
Whatever your background, it’s almost guaranteed that someone other than you will have previously sorted out the workshop set-up. In the jewellery and silversmithing industry, over-thinking your new set-up can never do too much harm; in fact it can save you from accidents, injury, unforeseen costs and legal pitfalls. This article looks at the big issues you must tackle when setting up.
Getting to grips with utilities
We’re talking about the basics here; gas, electricity and plumbing. It is essential that all work is carried out by qualified experts.
Electrics: All electrical work must be carried out by a qualified electrician, who is a member of a Competent Person Scheme through the Government approved registration body, NAPIT (National Association of Professional Inspectors and Testers), so that the work will comply with building regulations.
Plumbing: Plumbing must also be carried out by a qualified plumber who is registered through NAPIT
Gas: By law [The Gas Safety (Installation and Use) Regulations 1998] all work with natural gas fitting and appliances must be performed by a qualified engineer who is on the Gas Safe Register.
Portable or mobile gas equipment brings its own hazards and dangers. Go to the Health and Safety Executive website for a guide – Safety in Gas Welding, Safety and Similar Processes.
Contacts:
Safe extraction
Strict regulation applies to areas where fumes and dust are created. Equipment suitable for the safe removal of fumes or dust must be used, particularly during the following processes:
- Welding, soldering, burning, cutting etc
- Shot/bead blasting machine
- Woodworking machinery (including portable equipment)
- Machining of ceramics, carbon or other dust producing materials
Help: For advice on Local Exhaust Ventilation (LEV) Workplace Fume and Dust Extraction go to www.hse.gov.uk
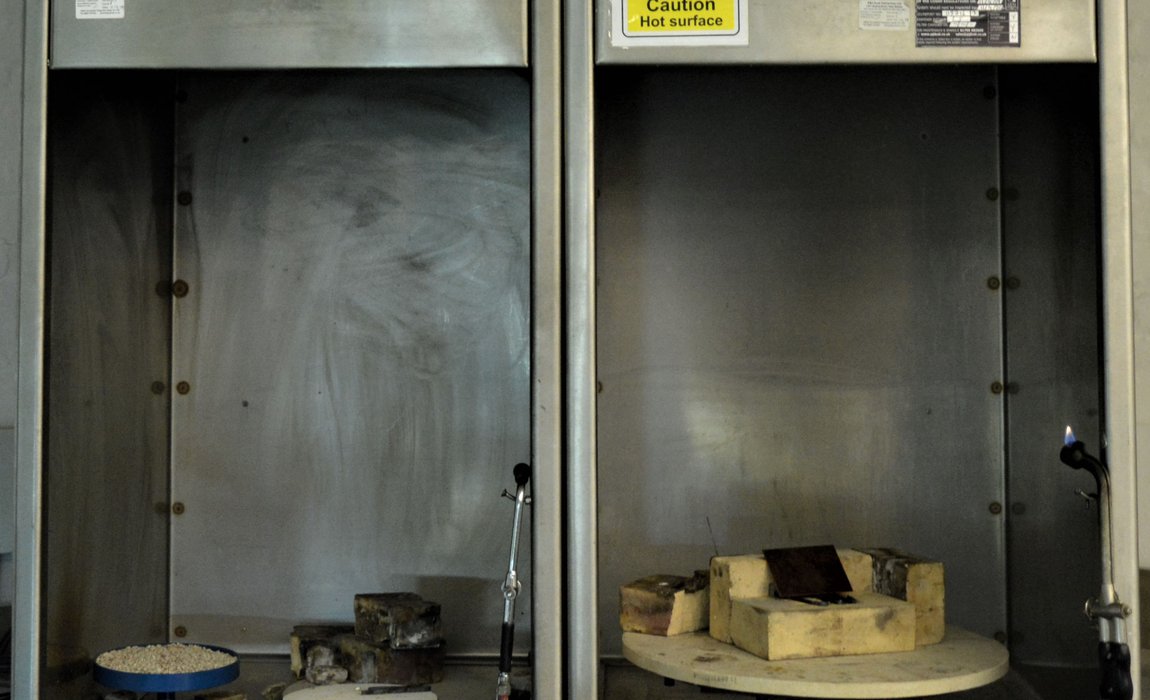
Writing risk assessments
Many procedures in a workshop environment carry a risk and an assessment must be undertaken on all operations and processes identified as such. The risk assessment identifies hazards, any rules and regulations surrounding the process and any controls which need to be put into place. Copies of these assessments should be available in the workshop and users must familiarise themselves with the risk assessment before starting work.
Help: Risk Assessment and Policy templates can be found on the Health & Safety Executive website www.hse.gov.uk
Making COSHH assessments
Every workshop contains potentially dangerous materials and awareness is vital. The Control of Substances Hazardous to Health (COSHH) regulates all materials which might be hazardous such as acids, solvents, chemicals, powders and enamels. Details of the nature of the substance should be obtained (usually in data sheet form from the manufacturer) and if thought to be hazardous, a COSHH form should be completed. This should contain detailed information about the nature of the substance and be kept on file in an accessible place. All users must read it before starting work.
Help: Find advice and a COSHH Essentials web tool at www.hse.gov.uk
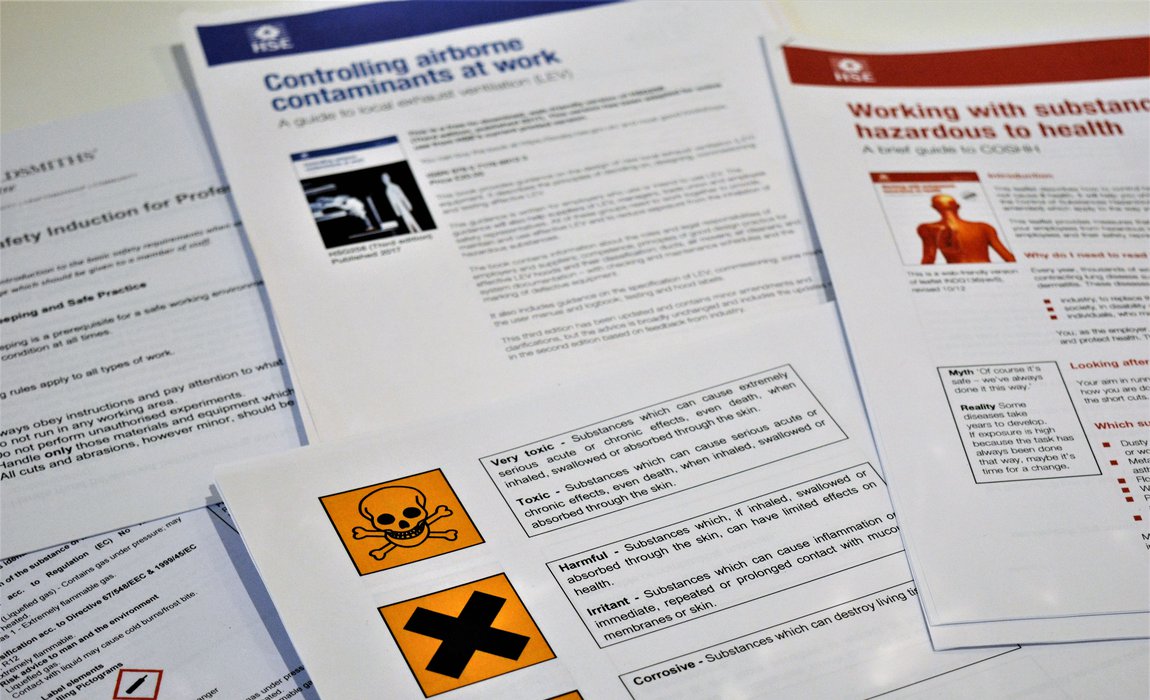
Working safely
Most workshop machinery is fitted with guards or safety devices designed to prevent access to dangerous parts. It’s tempting to remove guards from equipment, to seemingly save time and effort but the long-term risks far outweigh the quick fixes.
Whilst you have the responsibility to ensure all guards are in place, it must be emphasised that anyone who causes an accident by wilfully tampering with, removing, or not replacing a guard, is liable to prosecution under the Health and Safety at Work Act 1974 (sections 7 & 8).
Advice: For workshop safety advice go to www.hse.gov.uk and check out: The Simple Guide to the Provision and use of Work Equipment Regulations 1998 (PUWER). To see the Safety at Work Act 1974 in full go to www.legislation.gov.uk
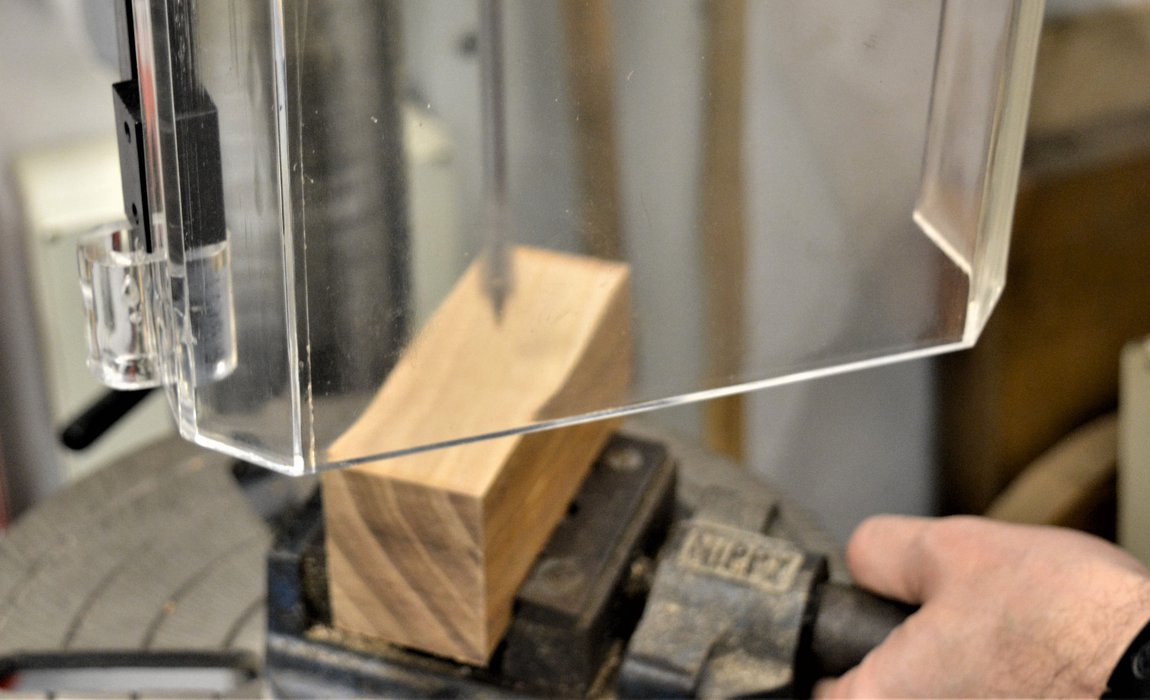
Protecting yourself
Personal protection is top of the list of workshop must do’s – the risks are great and the prospect of injury is never to be taken lightly. Machinery can be replaced – you can’t!
- Eyes: Workshops should be regarded as “eye protection areas” and each permanent workshop user must be supplied with a personal issue of safety spectacles or goggles. They must be worn whenever flying debris, or coolant splashes etc. might endanger the eyes. Eye protection should also be given to visitors where necessary.
- Clothes: Everyday clothes should be covered, while working in mechanical workshops, with overalls that fit closely at the wrists.
- Skin: Prolonged contact with oil, grease, cutting fluids etc. can cause skin problems. Barrier and cleansing creams should be available (and used!). Protective clothing must be laundered regularly.
- Hair: Long hair must be kept tied back securely.
- Jewellery: Wearing rings or dangling jewellery is very dangerous – remove before working.
- Hands: Wear suitable gloves when handling rough, sharp or dirty objects. However, near rotating machinery they must be removed.
- Feet: Protective footwear with strong soles must be worn for those involved in heavy lifting to prevent upward damage. Open or lightweight footwear should never be worn!
- Ears: Workshop users and visitors must wear suitable ear defenders or disposable earplugs near a source of loud/prolonged noise – particularly if it is over 85dBA (decibels (A)).
- First Aid: Every workshop should maintain a first aid box which should be checked regularly.
- Advice: For more information see: A Short Guide to Personal Protective Equipment at Work Regulations 1992 at www.hse.gov.uk
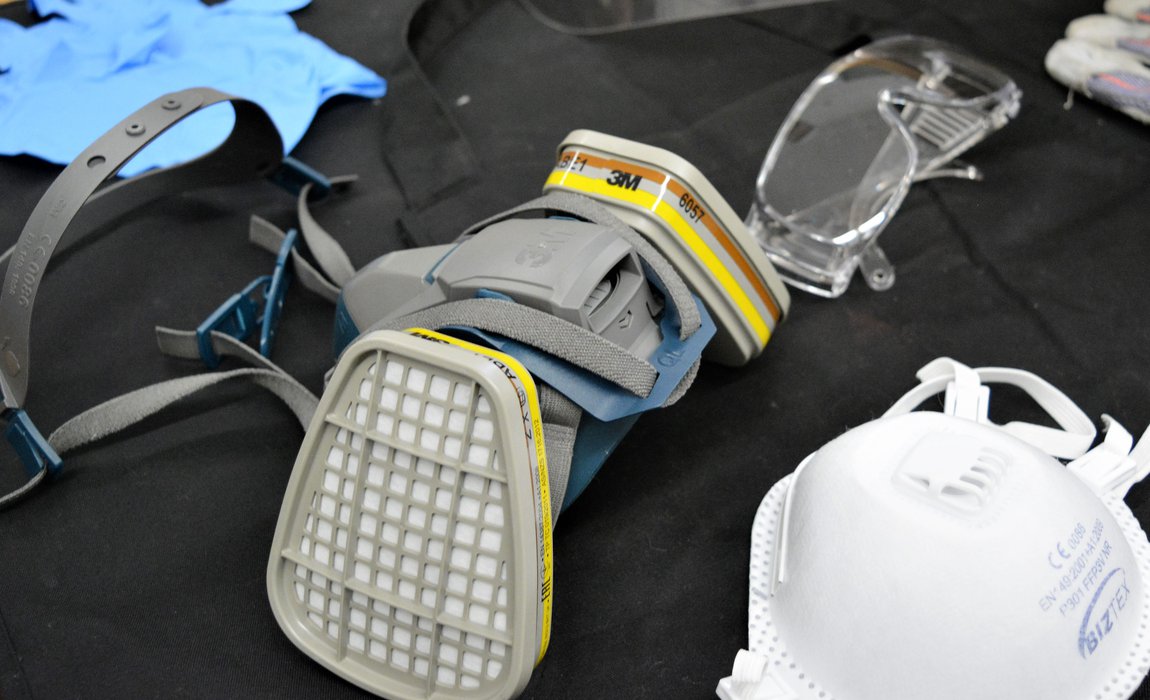
Handling chemicals
This is the one area which should not be tackled without in depth advice and expertise. Chemicals, whether storing, using or disposing of them, have their own set of unique risks and their own set of regulations. There’s every chance that if you get this bit wrong, your workshop could literally become a time-bomb. For those operating on a small scale all the safety and disposal criteria must not be ignored. Here are a few warnings and an indication of where to go for advice:
- Storage: When not in use, containers of flammable liquids should be kept closed and stored in suitable fire-resisting cabinets or bins, sited away from the work area and should not hinder escape routes. Flammable liquids should be stored separately from other dangerous substances that may increase the risk of fire.
- Use: Chemicals should always be kept in marked containers. Care should be taken not to mix solvents from different groups in the same tin.
- Disposal: Solvents should be disposed of in properly labelled containers. Waste cooling/cutting fluid must also be disposed of in the same manner - never poured into a drain.
- Advice: For more help with the storage and disposal of chemicals and chemical waste go to www.hse.gov.uk See: The Hazardous Waste (England & Wales Regulations 2005) at www.legislation.gov.uk
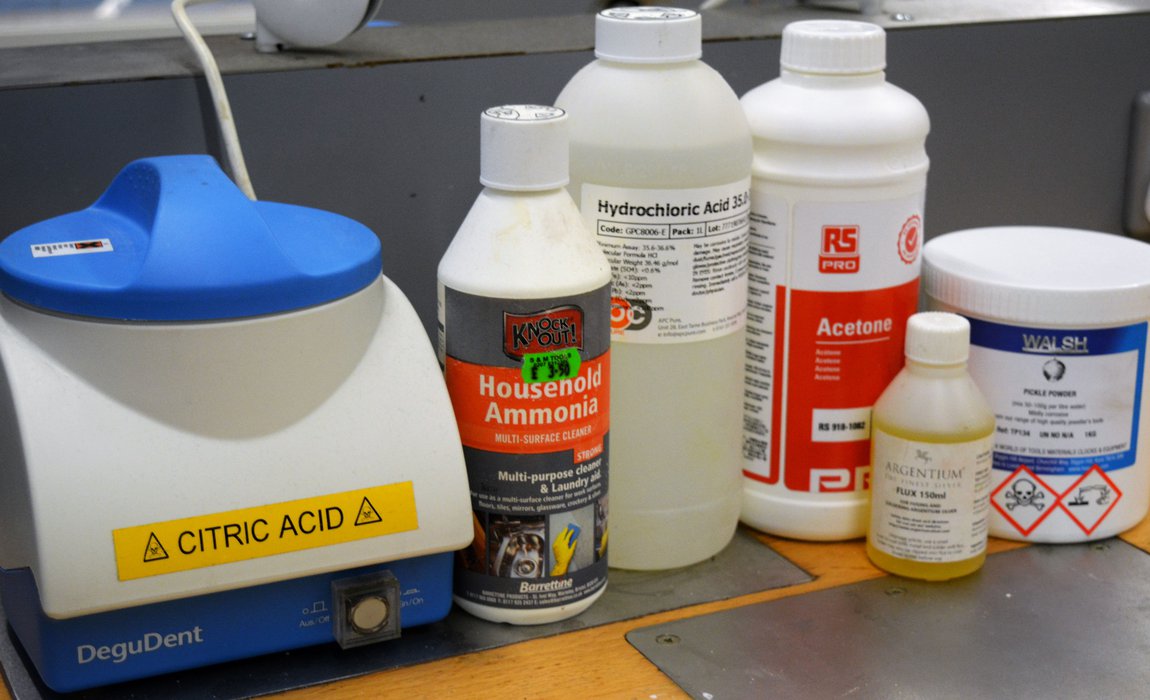
Further information
There are many reputable sources of information relating to the jewellery, silversmithing and allied industries. Whether you are trying to find information on technical skills, processes, materials, makers or inspiration some resources relating to health & safety can be found below:
The Goldsmiths’ Company Library relates specifically to gold and silversmithing, jewellery, assaying and hallmarking, precious metals, and the City of London and its guilds. The Library includes 8,000+ books and 15,000+ images, magazines, periodicals and journals, technical guides, films, special research collections, design drawings produced during the early and mid-twentieth century by British or UK-based craftspeople and subject files on a wide range of industry related topics. The Library is also responsible for the Company’s archives, which date back to the 14th century.
Health & safety related film content includes:
Goldsmiths’ Centre Workshop Film: Setting up your jewellery bench