Firescale and Firestain: What is Oxidisation and how can I stop it?
When heating precious metal, you may find that your work becomes discoloured with firescale or firestain. This article will help you understand the difference between the two types of oxidisation and what can be done to limit or remedy these common problems.
What is firescale and what is firestain?
When metal is heated its physical and chemical properties become altered. Firescale and firestain can occur when annealing, soldering, casting or heating metals which contain copper such as Sterling silver and lower carat golds.
Whenever you heat an unprotected precious metal which has copper as part of its alloy, such as gold or silver, you may find the surface has a black layer left on it. This is one of two types of oxide common when heating precious metal and is known as “firescale”. Firescale is a surface layer, is not permanent and is easily removed.
The second type of oxide is most common in sterling silver as this is a more permeable metal which allows oxygen to penetrate deeper into its surface. The oxidised copper atoms here leave a permanent red / purple tarnish or “firestain” within the metal. Unlike firescale, firestain is subtle in colour and is only truly noticeable when seen next to untarnished metal.
Just because you have firescale doesn’t mean you will have firestain, but this becomes more likely when a piece of precious metal becomes too hot for too long or is heated too many times. The amount that a piece is affected by firestain will depend on how hot the metal gets, how long it was heated for and how much copper is present.
“Firescale and firestain are both caused when an alloy containing copper is heated in air or oxygen forming Cu2O and CuO oxides.”
What causes firescale or firestain on my work?
Firescale and firestain can occur during any process which requires you to heat your metal including annealing, soldering and casting. They are most likely to occur when using a gas and air / oxygen torch to carry out these processes. When a precious metal is heated, the copper within the alloy reacts with the oxygen in your torch flame to produce copper oxides which can appear as a black scale on the surface of the metal (firescale) or as a red or purple discolouration within your metal (firestain).
The figure below shows a comparison of metals with firescale and firestain and where the particles of copper oxides sit. How deep the firestain oxides go depends on how far the oxygen has penetrated the surface when it was heated. The higher the temperature of the metal, the greater the rate of the oxidation and the thicker the layer can become.
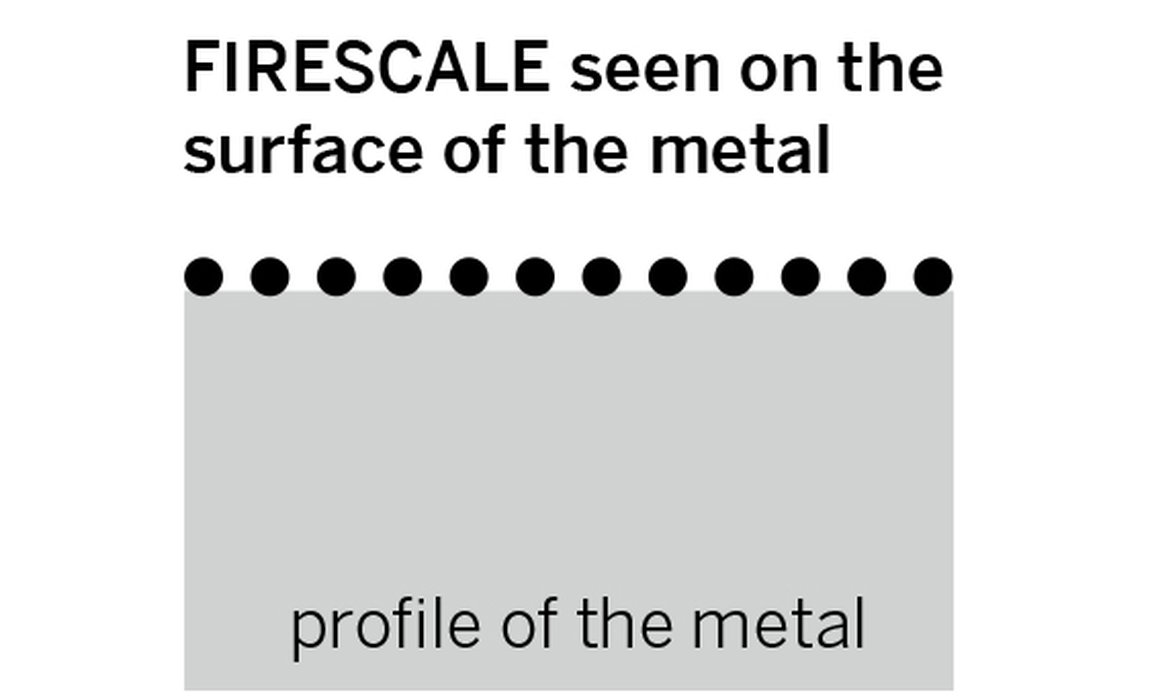
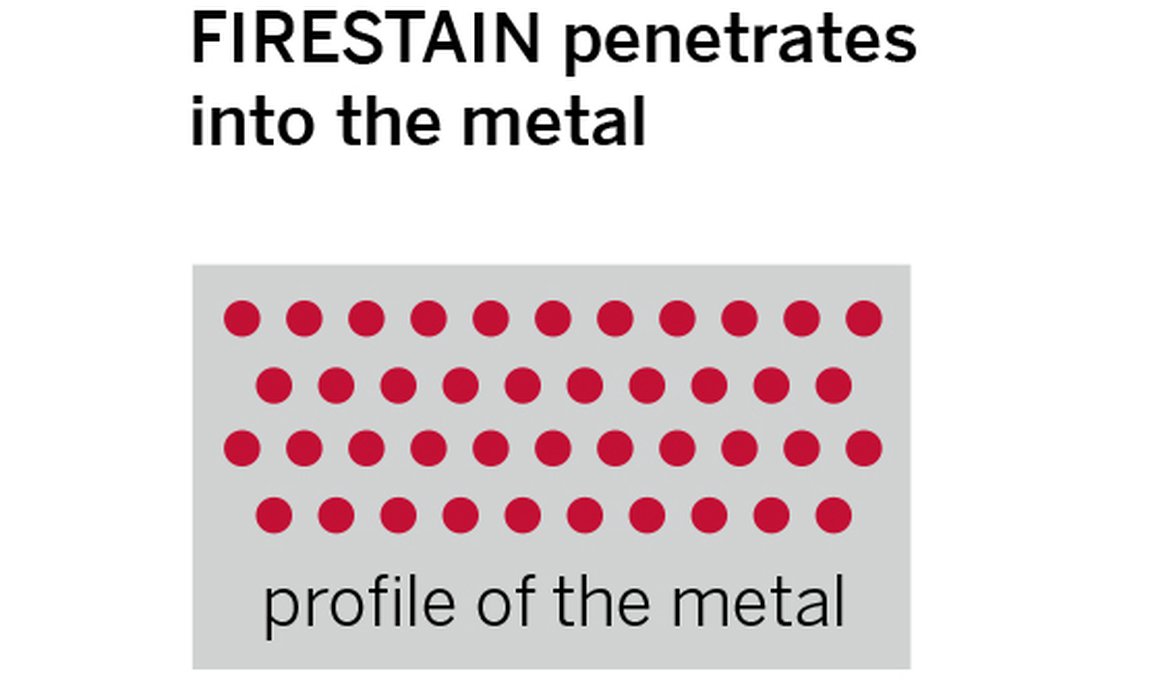
The more permeable a precious metal the more the oxygen can mix with the copper atoms causing firestain oxidisation. The colour of the tarnish will depend on the amount of copper within the precious metal alloy.
How can I prevent oxidisation from happening?
It is far better to prevent firestain than trying to deal with it once it has happened. In larger scale production it is possible to use a furnace with a protective, reducing atmosphere; an environment where gases such as hydrogen or carbon monoxide are used to remove oxygen, to limit oxidisation. Melting and casting operations can also take place in an inert, or chemically inactive, atmosphere.
This is, however, difficult to manage for individual craftspeople who are reliant on using a torch for their work. Understanding the different types of torch flame is integral to being a goldsmith and can help you to limit the possibility of firestain.
The three types of flame when using a gas and air torch are reducing, neutral and oxidising flames:
REDUCING FLAME | NEUTRAL FLAME | OXIDISING FLAME |
---|---|---|
A reducing flame has the lowest amount of oxygen and appears yellowish due to the presence of carbon or hydrocarbons that bind with and reduce the oxygen within the metal. This flame causes little or no oxidation if used but moving the flame away during the heating process may introduce oxygen which can allow oxidation. | A neutral flame has the precise amount of oxygen for burning when neither oxidation or reduction will occur. To achieve a flame with this balance of oxygen introduce just enough oxygen into your torch until the flame becomes slightly yellowish blue. | You can recognise the clear blue oxidising flame as it becomes shorter, darkens in colour and becomes louder than other flames due to excessive oxygen. This flame will cause firescale. |
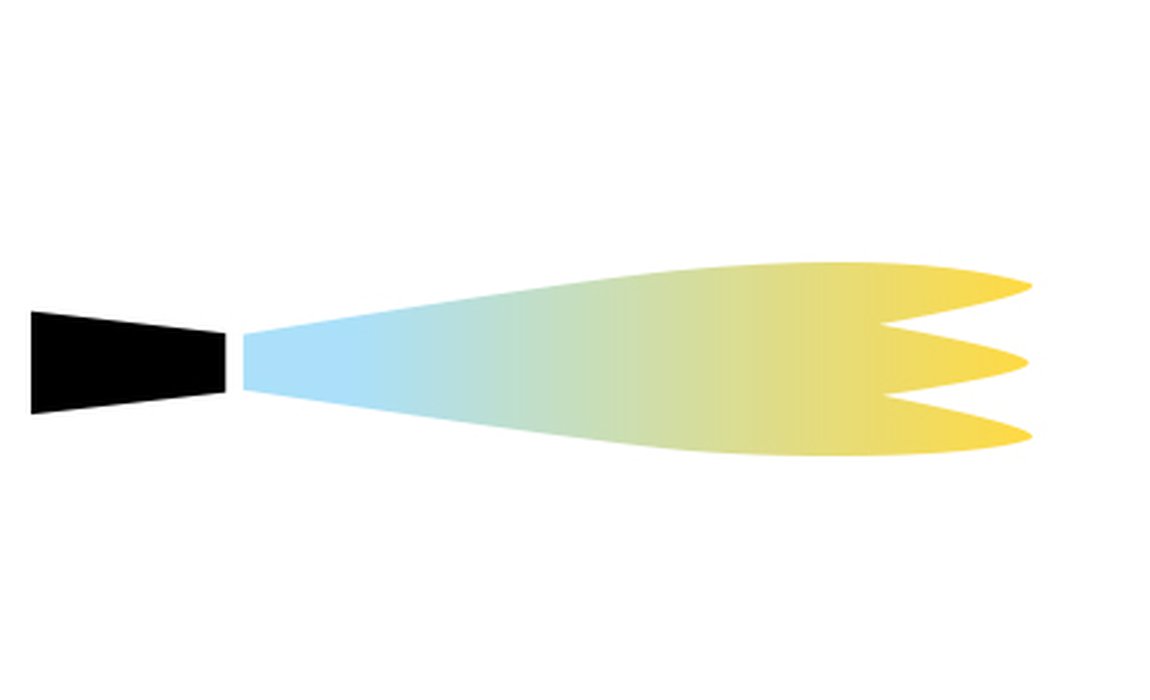
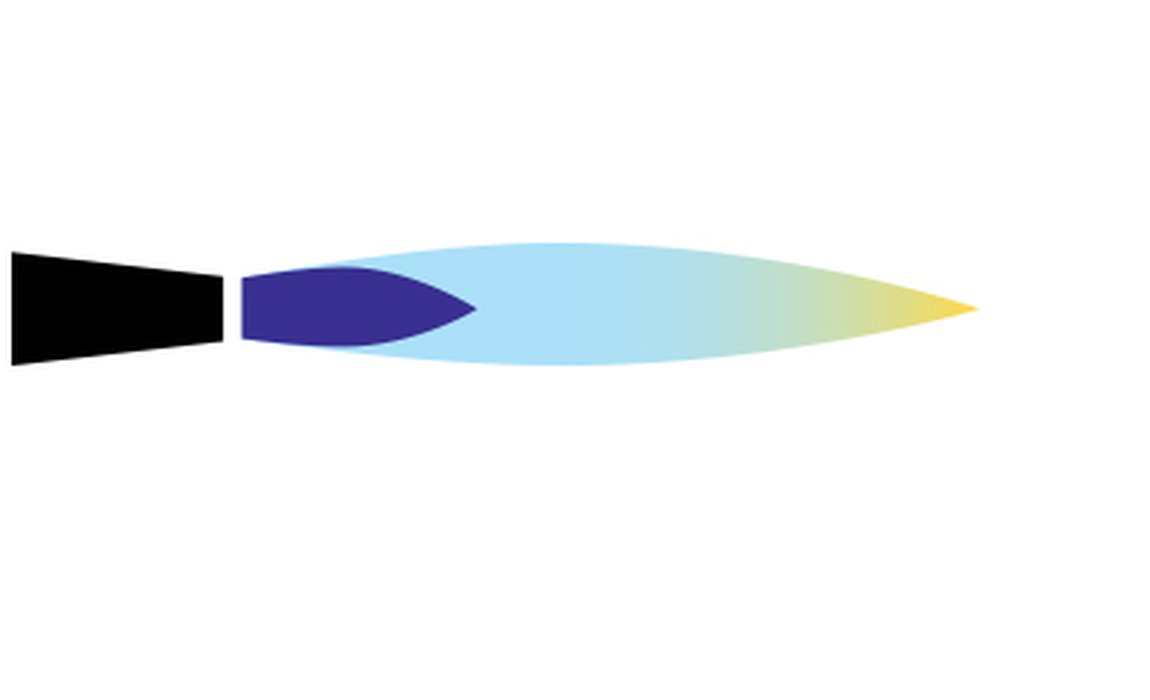
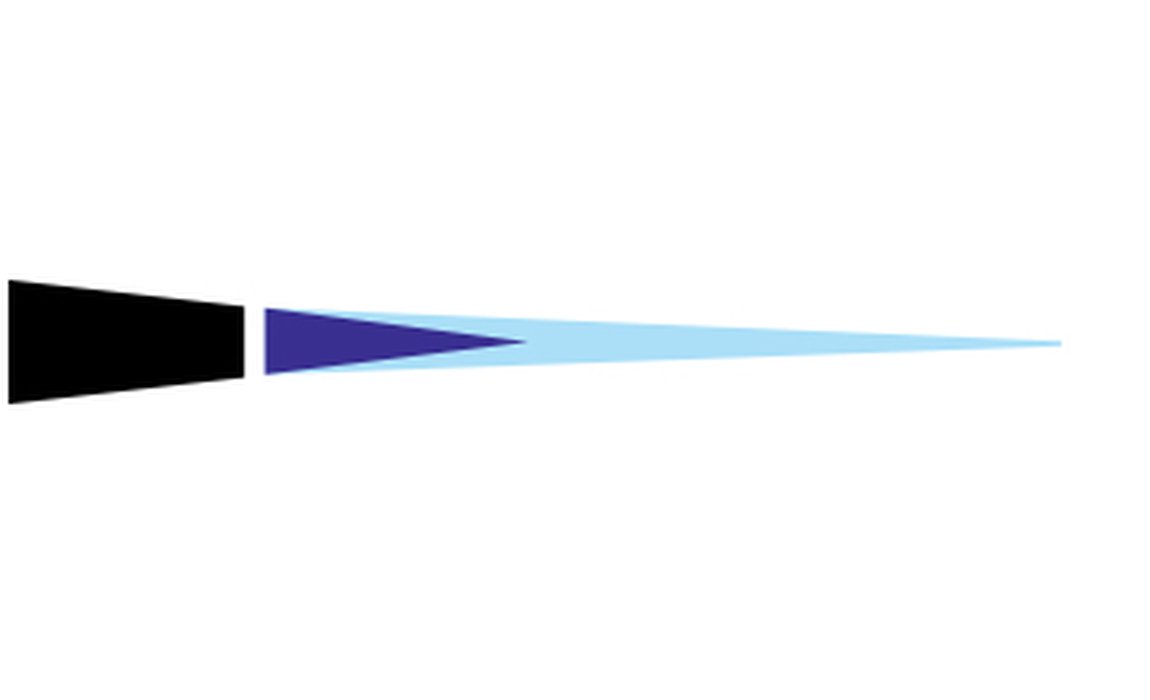
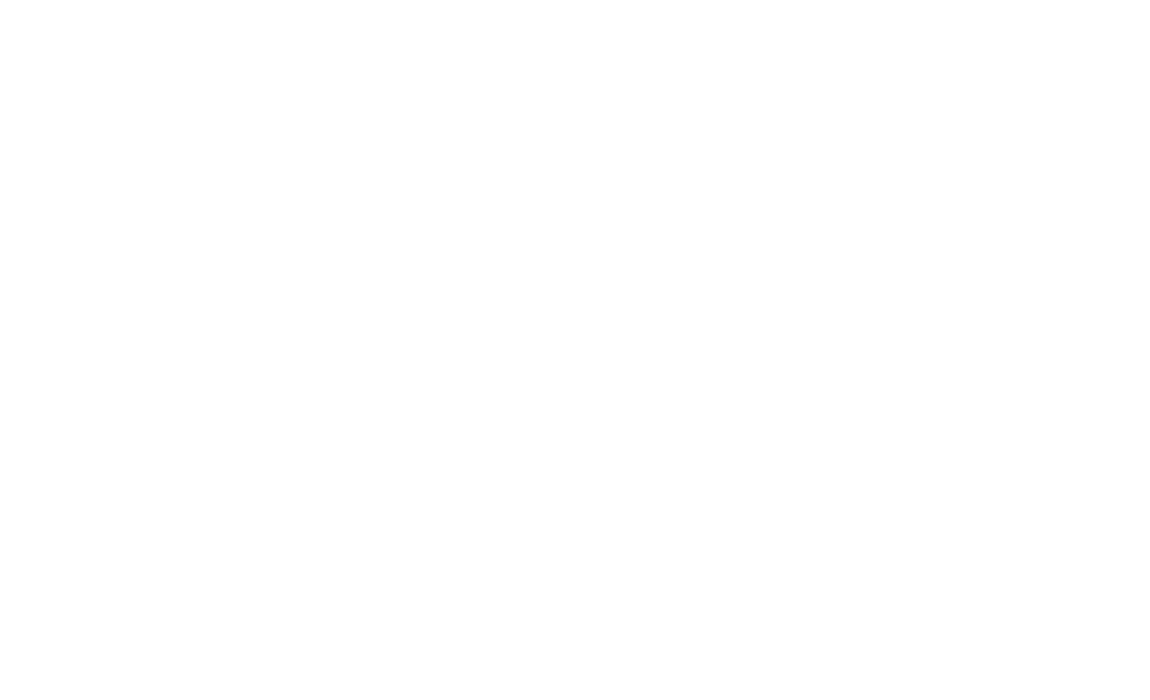
Both reducing and neutral flames are useful for soldering and annealing and the oxidising flame should not be used for this type of work. You can try to limit oxidisation from happening when heating your metal by using a neutral flame for annealing or soldering. It takes great skill to manage heating your metal using a neutral flame but doing so will help you to limit firestain.
Another way of helping to prevent oxidisation from happening is to use flux either in powder or liquid form. Flux is a solution that, when melted, will form a layer that sits on the surface keeping oxygen from reaching the metal. Covering the surface of your metal with flux prior to heating means that oxidation is prevented, and it can also absorb existing surface oxides into the flux which can then be washed off. Flux is also useful in helping to stop firescale forming within a solder joint which can interrupt the flow of the solder. There are various flux solutions that you may consider using and some of these claim to limit the likelihood of firestain, including Argo-tect within the UK.
You may also try using a charcoal block for soldering. When used in conjunction with a neutral flame this can help to reduce the amount of oxygen in the soldering area limiting oxidisation and the possibility of firescale and firestain. Charcoal blocks should be used in the same way as other soldering blocks, but you may find that your work heats up faster due to the material being a poor conductor of heat.
Precious metals are alloyed with copper in order to maintain the positive characteristics of the main metal including colour, hardness and malleability whilst adding strength. There are various alloys commercially available which claim to limit the likelihood of firestain through adding all altering their composition. These include Britannia and Argentium silvers.
My work has firescale or firestain. Can I get rid of it?
Firescale can be removed easily from the surface of your metal using safety pickle, pumice and a bristle brush.
If your work has firestain there are a few things that you can do to relieve the effects of the tarnish to a lesser or greater extent;
The appearance of firestain may lessen after using safety pickle but the stain is not truly gone and will return when filing, buffing or finishing the piece. Safety pickle removes the top-most layer of the oxide scale leaving a surface layer of copper-free precious metal. As it is only the top layer of particles which are removed any significant polishing, buffing or filing will reveal the underlying firestain as the top layer of metal is removed.
A fine layer of plating can cover up the firestain (and obvious solder seams) but is an additional cost and will wear off over time.
The only way to get rid of firestain permanently is to remove all affected metal until you pass through the level of the discolouration to the metal below. This is normally done using abrasive techniques including filing, sandblasting, emerying or polishing and can involve a significant loss of precious metal. It may also affect the shape and integrity of the piece and it will take significant additional processing and finishing. The success of this process will depend on the thickness of the firestain layer and the thickness and shape of your piece.
Conclusion and Further Information:
In conclusion, any time that you heat a precious metal with copper in the alloy you are at risk of oxidisation either as firescale on the surface or firestain within the piece. It is better to try and prevent oxidisation from happening rather than having to deal with firestain on your piece as this can require a lot of work, cost and loss of precious metal.
Further information and resources relating to firescale and firestain can be found below:
The Goldsmiths’ Company Library relates specifically to gold and silversmithing, jewellery, assaying and hallmarking, precious metals, and the City of London and its guilds. The Library includes 8,000+ books and 15,000+ images, magazines, periodicals and journals, technical guides, films, special research collections, design drawings produced during the early and mid-twentieth century by British or UK-based craftspeople and subject files on a wide range of industry related topics. The Library is also responsible for the Company’s archives, which date back to the 14th century.
Firestain related books or archived materials include:
- Untracht, O. (1987). Jewelry Concepts and Technology / Oppi Untracht. London: Robert Hale, pp.413 - 414: The Anatomy of a flame.
- Hill, B. and Putland, A. (2014). Silversmithing. Ramsbury: The Crowood Press, pp.54 - 55: Firestain.